工作機械の外装カバーとは?|用途・目的・必要とされる性能
工作機械に用いられる外装カバーとは、機械本体の筐体や制御盤、電装部、操作部などを覆う板金製の保護カバーを指します。工作機械用カバーには大きく分けて、可動部の摺動保護を目的とした「可動型カバー」と、機械全体を囲う「外装カバー」があります。
今回対象とする外装カバーは、一般的に摺動部を保護する可動型カバーとは異なり、工作機械全体の外観構成を担う固定型の部品であり、美観性、安全性、防塵性、防水性、さらには騒音対策など、複合的な機能を兼ね備える必要があります。
外装カバーが求められる理由(安全・美観・防音・防水)
外装カバーの目的は多岐にわたります。第一に、ユーザーの安全性を確保するため、可動部・電装部・熱源等への接触を防ぎます。次に、美観向上の目的で、製品としての見た目やブランドイメージを高める要素にもなります。また、内部構造を防塵・防水から守ると同時に、クーラント液や切削油が外部へ漏れないようにする構造が求められます。加えて、作動音を軽減する遮音構造や、熱源からの放熱を補助する設計も重要です。
主な適用分野(マシニングセンター/NC旋盤/複合加工機など)
外装カバーは、主に以下のような工作機械に用いられます。
-
マシニングセンター(MC):多軸の工具交換を伴う加工設備
-
NC旋盤:高速回転体を用いた切削加工設備
-
複合加工機:旋盤+フライスの複合機能を持つ高機能設備
-
放電加工機、研削盤などの特殊加工設備
これらの装置では、電装部や操作部の周囲に取り付けられた外装カバーが製品の印象を大きく左右します。また、大型機械の場合、カバーそのもののサイズが2,000mm以上にも及び、板金加工の設計精度・溶接技術・塗装品質が製品全体の完成度に直結します。
大型工作機械用カバーの製作における4つの課題
大型工作機械の外装カバーを製作する際には、設計・加工・品質管理・物流といった各工程において、一般的な板金加工とは異なる特有の課題が存在します。ここでは、実際の引合いや設計現場でよく見受けられる「4つの主要な課題」について整理し、それぞれがカバー製作の精度・納期・コストにどのような影響を及ぼすのかを説明いたします。
設計段階での板金知識不足による干渉・溶接不良
依頼者であるメーカーの設計エンジニアの方が板金構造に対する知見を持たない場合、以下のようなトラブルが多発します。
-
板厚や曲げの指定が現実の加工に適さない
-
組立時に干渉やズレが発生し、全体精度が損なわれる
-
アーク溶接やスポット溶接に不向きな構造が盛り込まれてしまう
特に外装カバーは見た目の品質も要求されるため、曲げや溶接の精度が外観に大きく影響を及ぼします。したがって、設計段階から板金製造の下工程を理解した構造設計が不可欠です。
大型・中型板金対応できる工場・設備の不足
外装カバーのサイズは1,000mmを超えることが一般的であり、部品点数が多い筐体の場合は2,000mmを超えるケースも珍しくありません。これに対し、多くの板金業者は大型製品に対応できる敷地、設備、搬送体制を持たず、結果として対応可能な企業が限られます。
-
加工エリアや塗装ブースのサイズ制限
-
板取りや曲げ時のハンドリング難易度
-
完成品の一時保管や出荷対応の限界
このように、物理的なキャパシティが品質と納期だけでなく、対応可否を制約しているのが現状です。
塗装品質の不安定さ(耐久性/粉体・溶剤の選定)
カバーの最終仕上げとして施される塗装は、外観・耐久性の両面において非常に重要です。しかし以下のような問題が発生しがちです。
-
粉体塗装と溶剤塗装の選定ミス
-
前処理工程の省略・不備による塗装不良
-
塗装ブース内の環境不備による色ムラ等
特にクーラント液や油煙が発生する加工現場では、塗装剥離やサビ発生を防ぐため、塗膜密着性や下地処理の工程品質が問われます。
アルミ溶接の困難さ(割れ・歪み・再現性)
工作機械の軽量化ニーズや見た目の美観性向上のためにアルミニウム(A5052など)を使用することが増えていますが、アルミ材は鉄系素材と比較して溶接の難易度が非常に高いです。
-
熱伝導性が高く、溶接歪みが発生しやすい
-
薄板になるほど溶接中の割れが発生しやすい
-
溶接技術者のスキル依存が大きく、品質のバラつきが発生
ファイバーレーザー溶接などの高度な制御技術を導入していない業者では、アルミ筐体の量産対応は現実的に困難となるケースも多く見られます。
高品質な外装カバー製作に求められる技術要素とは?
工作機械用外装カバーの品質は、単に板金加工だけでは決まりません。製品仕様に沿った設計、使用材質の選定、加工精度の確保、そして塗装や検査といった後工程まで、一貫して高いレベルで管理されていることが前提条件となります。ここでは、精度・美観・耐久性を求められる外装カバーにおいて、重要となる技術要素を5つの観点からご紹介します。v
構造設計・VE提案力(製造性とコストダウンの両立)
外装カバーは筐体の構造部でありながら、同時に「見せる製品」であるため、美観と機能のバランスが求められます。ここで重要なのが、製造現場の視点を反映した構造設計とVE(Value Engineering)提案です。
例えば、以下のような設計支援が、製造前の設計段階で行われると、QCDの改善に大きくつながります。
-
部品点数の削減による組立工数の低減
-
歪み抑制のための溶接位置・方法の見直し
-
板厚や材質の適正化による材料コストの最適化
逆に設計者が図面段階で板金構造や現場工程、製造現場のキャパシティを理解していないと、製造現場でのやり直しが発生し、納期遅延や品質不良につながる恐れがあります。
材質別対応ノウハウ(SPHC・アルミ・SUSなど)
工作機械カバーには、使用用途に応じてさまざまな材質が選定されます。たとえば、
-
SPHC:汎用性が高く、溶接・塗装適性も良好な鉄鋼材
-
SUS(ステンレス):耐食性が求められる機器向け
-
アルミ(A5052など):軽量・高意匠性を求められる製品
これらの素材に適した加工条件や溶接手法を熟知しているかどうかが、製品の品質と安定生産性に直結します。
寸法精度・歪み対策・溶接管理の技術
外装カバーは、単なる箱形状ではなく、複数の板金部品の組立構造で成り立っています。つまり溶接による熱歪みが累積すると、最終製品で大きなズレが生じ、組立工程に支障をきたす原因となります。
そのため、以下のような技術管理が求められます:
-
熱歪みを計算に入れた溶接順序の設計
-
板金展開図と溶接手順・溶接ロボットプログラムの精緻な整合性
-
製品精度の品質保証・検証
特に溶接箇所が外観に表れる構造では、見た目にも影響するため、高い技術レベルが必須です。
粉体・溶剤塗装の選定と塗装ブース管理
塗装は外装カバーの最終品質を決定づける重要工程です。粉体塗装・溶剤塗装の選定はもちろん、前処理・乾燥・ブース環境まで含めた一連の管理体制が不可欠です。
例えば:
-
粉体塗装:耐候性と厚膜が求められる屋外仕様に適する
-
溶剤塗装:高意匠性や細部への塗装が必要な筐体に最適
これらに加え、静電気対策やゴミ噛み防止など、塗装ブースのクリーン性確保も求められます。
ストックヤード・搬送管理などの出荷体制
工作機械用の外装カバーはサイズも重量も大きいため、製造後の保管や搬送までを含めた物流対応力も重要です。とくに以下のような点が評価されます。
-
数十~百台単位の製品保管が可能なストックヤード
-
大型パレットや丁寧な梱包など搬送体制の柔軟性
-
出荷前検査や塗装面保護のノウハウ
これらは「出荷までを含む品質保証体制」として、発注者の皆さまの安心感を決める判断軸になります。
筐体設計・製造.COMだからこそ可能な工作機械カバー製造体制
工作機械向けの外装カバーにおいて、筐体設計・製造.COMを運営する岡部工業株式会社が選ばれる理由は、「高精度な板金加工技術」と「一貫対応可能な生産体制」にあります。特に、1,000mmを超える中型~大型サイズの製缶板金においては、設備・設計・工程管理の総合力が求められます。
1,000mm~2,000mm超の大型板金製作に対応
中型~大型サイズの筐体カバー製作においては、物理的な加工スペースと対応設備が不可欠です。岡部工業では2,000mm級のカバー製作を日常的に行っており、NCTレーザー複合機(ACIES)や大型プレスブレーキを活用した24時間対応の板金ラインを構築しています。
また、アルミ・鉄・SUSなど材質を問わず多様な素材に対応できる体制が整っており、板厚やサイズに応じた最適工程を社内で完結可能です。
アルミ溶接に最適なファイバーレーザー溶接機を4台保有
アルミは熱伝導率が高く、溶接時に割れや歪みが発生しやすい難加工材です。岡部工業では、アマダ製ファイバーレーザー溶接ロボット「FLW-3000」「FLW-4000」計4台を導入しております。フィラーワイヤーの自動制御やプル軸モーターによるワイヤー再調整機能により、安定した連続溶接と断続溶接が可能となっています。
これにより、従来難しかったアルミの量産対応や、溶接箇所の美観・強度確保が両立され、外装カバーに求められる品質に応えています。
クリーンルーム塗装×粉体・溶剤対応×前処理含む品質管理
塗装工程では、クラス10万のクリーンルーム内塗装ブースを保有し、粉体・溶剤のいずれにも対応。塗装前にはDIP式前処理装置+純水洗浄+焼付乾燥炉を備えたラインが組まれており、密着性や耐久性の高い塗装品質を実現しています。
また、大型塗装品についてはバッチ式ラインで柔軟に対応し、外観品質の求められる外装カバー製品にも安心して適用できます。
ポンチ絵からの設計支援と部品点数削減・VE提案
岡部工業では、「図面が完璧に揃っていない」状態でも、ポンチ絵・仕様書・機能要件のヒアリングをもとに設計提案が可能です。板金設計に精通した技術者が3D CAD(SolidWorks)を活用し、以下のようなVE提案を行います:
-
部品点数を減らす構造変更
-
作業性を向上させる加工順最適化
-
板厚の見直しによる材料費削減
これにより、加工コストの最適化と現場対応力の強化を同時に実現しています。
100台以上保管可能な大型ストックヤード完備
工作機械向けの外装カバーは、製作後すぐに納品されるとは限りません。複数台の生産や客先都合による納期調整など、柔軟なストック体制が必要となります。
岡部工業では、100台以上の筐体製品を保管できる広大なストックヤードを完備しており、出荷調整やロットごとの分納にも柔軟に対応可能です。出荷管理、搬送体制、梱包設計まで含めた一貫した物流管理力は、他社にはない大きな優位性です
工作機械用カバー製作の事例紹介
ここでは、筐体設計・製造.COM(岡部工業株式会社)が実際に手掛けた、工作機械向け外装カバーの代表的な製作事例を2件ご紹介いたします。
【事例1】アルミ筐体(A5052P)|ファイバーレーザー溶接による高意匠性の実現
本事例は、全体がアルミ材で構成された外装カバーであり、溶接による熱変形や割れが起こりやすい条件下にある製品でした。通常のファイバーレーザー溶接機では、フィラーワイヤーの位置制御が難しく、連続溶接が困難でしたが、岡部工業では自動フィラー制御対応の第5号機を導入することで、断続かつ安定したアルミ溶接を実現しました。
>>工作機械用アルミカバー(ファイバーレーザー溶接)製品事例はこちら
【事例2】大型SPHCカバー|1,700×2,300mm級サイズへの防水・塗装対応
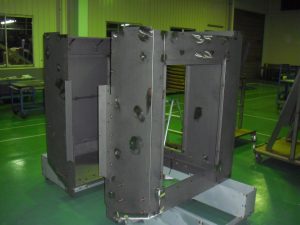
工作機械用大型カバー
この製品は、マシニングセンターに取り付けられる大型の製缶板金製カバーで、全体のつなぎ目に段差や歪みが生じないよう、溶接時に都度寸法を確認しながら作業を進める必要がありました。特に、内部からのクーラント液漏れを防ぐために、防水検査工程を追加し、機能面でも厳しい要求をクリアしています。
※掲載可能な事例は一部となっております。その他、NDA(秘密保持契約)により公開できない実績も多数ございます。詳細については、お問い合わせください。
大型工作機械の外装カバー製作なら、まずは設計段階からご相談を
工作機械用の外装カバーは、単なる板金製品ではなく、装置の品質・安全性・外観を左右する極めて重要な構成部品です。特に1,000mmを超える中大型筐体のカバー製作では、設計段階から製造性や塗装適性、搬送や設置後の耐久性までを視野に入れた対応が不可欠です。
そのため、筐体設計・製造.COM(岡部工業)では、初期の設計段階からのご相談を強くおすすめしています。
これから工作機械用の外装カバーを設計・調達される方、既存の仕入先で品質や納期に課題を感じている方は、ぜひ一度、筐体設計・製造.COMへご相談ください。
部品点数の多い複雑筐体から、意匠性を重視した精密カバーまで、設計から出荷まで一気通貫でサポートいたします。