>>板金加工から塗装・組立までワンストップ対応!岡部工業の次世代工場「板金ソリューションファクトリー」
筐体設計におけるポイントまとめ
筐体設計とは、目的・用途・使用環境など様々な要求を満たした上で、製作現場である下工程についても考慮をしなければならない、全体最適な視点が必要な仕事です。
筐体製作では、生産現場からの設計サポートと高度な生産技術力が量産体制の場合は特に求められます。
部品点数を1つ減らしたり、工程を1つ短縮するだけでも、量産での筐体製作の場合は大きなコストダウンや納期短縮につながるのです。
ここでは、筐体設計のポイントについて解説していきます。
筐体とは
筐体とは、精密板金や製缶板金など板金加工品の組立加工品のうちの1つで、電機機器や機械、装置を内蔵する箱のことを意味します。
「筐体」という大きなくくりの中には、
- 手のひらに収まるような小型の筐体 ⇒ スマートフォンやパソコン
- 各種盤や什器として使用されるキャビネット ⇒ 制御盤・分電盤・配電盤
- エンジンなどを内蔵 ⇒ 自動車や飛行機のボディ
など、小型から大型まで様々なサイズの筐体が存在します。
物によっては、「ボックス」「ケース」「ラック」とも呼ばれます。
筐体設計とは
筐体設計とは、筐体の使用目的・環境に対して、必要とされる形状や機能を抽出し、筐体を具現化していくプロセスを指します。
そもそも、「筐体設計」は「機械設計」のうちの1つであることがほとんどです。
ちなみに機械は「エンジンやモーターなどの動力によって一定の動きを繰り返し行うもの」と定義され、各種設計は以下のように説明されます。
- 機械全体を設計すること:「機械設計」
- 中身のエンジンやモーターなどの作動部の設計:「機構設計」
- 作動部以外の部分の設計:「構造設計」
- 構造設計のうち、ネジやビス、蝶番などの部品の設計:「部品設計」
- 構造設計のうち、外殻部分の設計:「筐体設計」
筐体設計のプロセスにおいては、使用目的・環境に応じて筐体の形状を考案したり、変更したり、機能を付与したりすることもあります。
しかしその場合、別の解消すべき課題が生じる場合が往々にしてあります。
筐体設計は、それらすべての条件を満足させるように調整を図っていく過程とも言えます。
筐体設計の目的
筐体の役割は、筐体内に収められている機器や装置、機械を保護することにあります。
そのため、筐体設計の目的は、筐体が実際に使用される目的や環境によって大きく影響されます。
筐体設計において目的となる項目には「耐衝撃」「防塵」「耐圧」「防水」「騒音対策」「ノイズ対策」「温度対策」「耐光」「密閉対策」などがあります。
特に屋外で設置される制御盤のような大型筐体の場合には、防水・防塵の規格であるIP規格が適用され、防錆性・防食性を高めるために塗装を行います。
また、近年は製品のスペックが上昇しているため、製品・筐体に対し「軽量化」「デザイン性」「安全性」「耐久性」「納期」「コスト」などが必要となる場合もあります。
筐体設計は、複雑かつ難易度の高いものになってきているのです。
筐体に使われる材質
筐体は、主に金属や樹脂によって製作されます。
日用品の場合は使用者が一般消費者になるため、軽量化のために樹脂(プラスチック)によって筐体が作られることも多くあります。
しかし、多くの産業用筐体は製品への要求特性が多いため、ほとんどが金属を用いた製缶板金加工にて作られています。
代表的な素材には、一般的な鉄だけではなく、SPCC、SPHC、SECC、SUS、アルミなどもあります。
これらの素材は剛性が高いため、金庫筐体、ATM筐体など防犯の必要がある筐体に適しています。
また、耐候性が高いため、屋外で使用される筐体にも適しています。
さらに、専用金型が必要な樹脂筐体と比較して金属筐体は一般的には金型が不要で汎用機で製作ができるため、多品種少量生産にも対応が可能です。
筐体設計・製作の流れ
筐体設計・製作は、以下の流れで進んでいきます。
- CAD設計
- CAM
- 抜き加工
- 曲げ加工
- 溶接加工
- 組立加工
- 塗装・表面処理
- 検査
以下でも説明しますが、この中で最も重要なのが①のCAD設計です。
まだ製品がない状態の中で、筐体板金の加工の難易度・精度・コスト・リードタイムなどを考慮した上で、さらに加工者に対しては設計者の意図が伝わりやすい図面を作成しなければなりません。
また、CADデータををもとにCAMで加工プログラムが作成されるので、筐体設計・板金設計こそが筐体設計の頭脳と言っても過言ではありません。
筐体設計のポイント
筐体設計におけるポイントは、以下の通りです。
- 様々な要望に耳を傾ける
- あらゆる人とのコミュニケーション
- 全体最適の視点
筐体設計では、お客様から仕様について要望が生じるだけではありません。
BtoBの製造業ならではですが、お客様のお客様からも要求が出る場合があります。
例えば、筐体内部の温度上昇を避けるために取り付けたとき、冷却ファンの動作音が周囲に騒音となってしまうなど、別の課題が準じて生じてしまうケースがあります。
この場合では、「冷却ファンを周囲に影響を及ぼさない箇所に設ける」「ヒートパイプなど、冷却ファン以外で排熱を行う」などの設計を行うことで、筐体内の冷却と騒音を解決することができます。
さらには上記で説明したとおり、筐体設計における要望は「デザイン性」「安全性」「コスト等」など千差万別です。
様々な要望に耳を傾けることが、筐体設計の重要なポイントです。
また、様々な要望に耳を傾けるだけでも行けません。
「こっちの意見を通せば、あっちの要求は通らないから…」という形で、すべての要求を満たすことができるのは稀なことです。
そのため、社内外のあらゆる人とのコミュニケーション能力も非常に大切です。
交渉力、説得力といった対人スキルも筐体設計には必須となります。
つまり、筐体設計では全体最適の視点が必要になります。
筐体が使用される目的や環境、役割を理解し、筐体の役割のうち何が優先事項となるのかを見据えた上で、板厚や曲げの種類等の加工方法、外注先等を選定する必要があり、その方針を周りの方々に納得してもらうためにコミュニケーションを取る。
こうした筐体製作のプロセスにおいて、全体的なバランスを担う舵取り役が筐体設計者なのです。
筐体設計に多い課題
筐体設計には全体最適の視点が必要なため、様々な課題が付きまといます。
結論を先に申し上げますと、筐体設計における課題は「板金設計などの筐体製作の下工程に熟知しており、全体最適なバランスを取ることができる設計者や製作メーカーでなければ、最適な筐体設計ができないこと」です。
ATM・自動精算機・通信機器などの大型筐体には部品点数が400点以上となる複雑な筐体もあり、それらは溶接により組み立てなければなりません。
したがって、部品点数の多い複雑な大型筐体の場合は、溶接熱による歪みを最小限にとどめるような構造設計が必要となります。
部品点数が多くなるほど、溶接による少しの歪みやズレが累積し、最終的な組立品になった際に大きなズレを生み出してしまうのです。
つまり、筐体の製造は設計の段階から溶接方法まで計算に入れなければならないのです。
溶接の種類も「アーク溶接」「MIG溶接」「YAG溶接」など多くの溶接方法があるため、どの溶接方法であれば溶接熱による歪みを少なくすることができるかを考慮し、溶接方法を細かく指定しなければいけません。
歪みが大きくなってしまうと、嵌め合い部品や窓・扉の開閉等に影響を与えてしまい、筐体製品としては欠陥を持つことになってしまいます。
加えて、多くの大企業には、溶接や加工のノウハウを熟知した設計者がいないという課題もあります。
多くの設計者は「こういう筐体をこうやって使いたい!」「これくらいのサイズでこんな特性のある筐体がほしい!」と考えるものですが、実際にそのような筐体を設計・製作となると、どうしても筐体の目的や役割に視点が偏ってしまいます。
また、板金の穴の位置・曲げ度合い・加工工程のプロセスといった筐体製作の下工程を無視した筐体を設計してしまうことも多くなってしまいます。
そのため、無理難題な筐体製作を下請け業者に依頼してしまうケースが多く、結果としてなかなか筐体を製作どころか、試作すらもできないようなことも多々あります。
筐体 設計・製作.comならではの筐体設計
筐体 設計・製作.comでは、これまでに数多くの大型精密筐体の設計・製作をしてきました。
そんな当社ならではの筐体設計としては、以下のポイントが特徴としてあげることができます。
実際の板金加工・溶接・塗装という下工程を理解した板金設計が可能
筐体設計においては、筐体製作の工程ごとに展開した際の作業性(加工・溶接・組み立て・塗装)を加味した設計を行うことで、コストダウンや品質改善に大きな効果を及ぼします。
専門の筐体設計者や板金設計者でない方が筐体設計を行うと、無理のある設計条件を盛り込んでしまうことが多々あります。
その場合は、加工・製作時の作業性低下による歩留りの悪化や、溶接不良、塗装不良などの品質低下につながり、結果として高い品質の大型精密筐体を作ることができません。
つまり、筐体設計においては、実際の加工・製作という下工程を理解した板金設計・筐体設計を行うことが、最適なコストで高品質な大型筐体を作ることに直結します。
筐体 設計・製作.comでは、創業以来あらゆる大型精密筐体を設計・製作して培ったノウハウと、それにもとづく最適な工程作業性をベースとした筐体設計と行うことができます。
穴の加工方法や溶接方法の変更、部品点数を少なくした加工法等を熟知した、板金設計段階から高精度かつ最適な部品製作を積み重ねることで、最終的に歪みやズレのない高品質な大型精密筐体を製作することができます。
ファイバーレーザー溶接ロボットによる高い生産性&高度な技術力
筐体設計・製造.COMでは最新のファイバーレーザーロボット溶接機を導入しており、薄板板金の溶接加工を得意としています。
薄板板金の溶接となると、作業者の技術力によって精度のばらつきが生まれがちですが、ロボット溶接を行うため、精度のばらつきがなく、かつ、高い生産性のもと薄板溶接を行うことができます。
これにより、精度の高い、量産品の薄板板金の溶接が可能となります。
圧倒的な設備力により、様々な加工方法の中から最適な工程を選定可能
筐体設計・製造.COMではファイバーレーザー溶接の他にも、CO2溶接・TIG溶接・YAG溶接など、あらゆる溶接手法を取り揃えています。
また溶接だけでなく、プレス機、プレスブレーキを多数保有しており、さらにNCTレーザー複合機などの最新機により24時間の生産体制をとっております。
筐体設計においては、板金設計などの筐体製作の下工程に熟知しているだけではいけません。
重要なのは、いかに最適な加工工程を選択できるかということにあります。
そのためには、どのような設備があって、どのような加工に対応できるのかが非常に重要と言えます。
筐体設計・製造.COMでは、創業精神である「進取の精神」のもと、新しいものはどんどん取り入れ、それを活かしてさらなるレベルアップを目指しています。
近年はお客様が筐体に対して抱える課題も複雑化していますが、そのような難解な課題に対しても、我々が最新鋭の機器を取り入れて、常に技術力に磨きをかけることで、数ある選択肢の中からお客様に対して最適な加工工程を提案できるように努力しております。
ポンチ絵や機能、外観形状等の要求仕様のみで筐体設計が可能
筐体設計・製造.COMでは、お客様からの要求仕様を元に、筐体の設計・製造を行うことも可能です。
まずは、ポンチ絵や筐体の機能、外観形状などの要求仕様がわかるものを、イメージとして当社へお伝えいただきます。
次にヒアリングを行い、お客様のイメージと当社の認識のすり合わせを行います。
このように綿密なすり合わせを通して、筐体の仕様が共通認識として確立した後に、3D CADを用いて筐体設計を行います。
また、筐体設計・板金設計については、板金加工のノウハウを熟知した設計者が行います。
お客様への積極的なVE提案によってコストダウンに貢献
筐体設計・製造.COMでは、お客様とのイメージ擦り合わせの段階において、筐体・板金設計のプロフェッショナルとして積極的なVE提案をいたします。
ただ お客様の要求仕様に応えるだけではなく、コストや納期面といった側面も踏まえた上で、お客様に満足して当社の筐体をお使いいただけるように、常によりよい提案をしております。
板金設計のノウハウに合わせて、生産性の高い機器を積極的に活用することで、お客様のご要望に柔軟に応えて参ります。
筐体 設計・製作.COMではの筐体製作の実績
いままで筐体設計・製造.COMでは、「ボックス」「キャビネット」「ケース」など、多種多様な形状の筐体を製作しています。
以下は、当社が製作してきた筐体の実績です。
- 通信機器向け筐体 サイズ 1,900 x 600 x 800 50台/月
- 自動精算機向け筐体 サイズ 1,400 x 600 x 500 50台/月
- ATM向け筐体 サイズ 1,600 x 900 x 500 500台/月
- ATM向け筐体 サイズ 1,300 x 900 x 500 400台/月
- ATM向け筐体 サイズ 1,600 x 700 x 450 300台/月
- 医療機器筐体 サイズ 500 x 500 x 200 100台/月
- 現金処理機向け筐体 サイズ 600 x 600 x 150 600台/月
このほかにも半導体や産業機械、介護、パスゲート、農業、土木建築、アミューズ系など、多岐にわたるジャンルの問合せが現在も殺到しております。
筐体設計は、筐体設計・製造.comにお任せ!
筐体設計について、おわかりいただけましたでしょうか。
筐体設計には、目的や用途、使用環境、精度、特性、コストなど数多くの要求を満たした上で、実際の製作現場である下工程についても最適な工程を考慮しなければならない、全体最適な視点が必要なプロフェッショナルな仕事です。
そのような筐体製作には、生産現場からの設計サポートと、高度な生産技術力が、量産体制の場合は特に求められます。
部品点数を1つ減らしたり、工程を1つ短縮するだけでも、量産での筐体製作の場合は大きなコストダウンや納期短縮につながるのです。
筐体設計・製造.COMを運営する岡部工業株式会社は、群馬県から発信するグローバル板金ソリューションカンパニーとして、お客様の板金や筐体に関するお困りごとを解決いたします。
中国工場とも連携した幅広いネットワーク、最新鋭のファイバーレーザー溶接ロボットを代表とした圧倒的な設備力、さらに創業以来から大手メーカーとの取引によって積み重ねてきた板金設計・筐体設計のノウハウを活かして、お客様の課題を解決していきます。
筐体という製品は、一度製作したら長く使用するものです。だからこそ、安心安全かつ使い勝手がよく長持ちする製品であるべきです。
設計初期の段階から当社にご相談いただけましたら、当社にて生産技術的な要素を設計に取り込んだ上で、筐体製作を行います。
そうすることで、当社の金型や設備、製造ノウハウを盛り込んだ筐体を製造することが可能となり、低コストで品質の良い筐体を短納期で製作する事ができます。
筐体設計に少しでもお困りの方は、まずは筐体設計・製造.COMにご連絡ください。
板金ソリューションカンパニーとして、あなたのお悩みを解決いたします。
>>【無料】技術ハンドブックはこちらから
精密板金の塗装から組立まで、すべてお任せください!
岡部工業の新工場では、筐体板金の塗装から組立までを一貫対応するワンストップ生産体制を実現しています。自動コンベア式とバッチ式の両方に対応可能な広大な塗装エリアを備え、お客様のさまざまなニーズに柔軟に対応します。
>>板金加工から塗装・組立までワンストップ対応!岡部工業の次世代工場「板金ソリューションファクトリー」
精密板金 塗装・組立までのワンストップ生産体制
岡部工業の塗装工程、組立工程についてご紹介いたします。
クラス10万のクリーンルーム内のコンベア式塗装ブース
クリーンルーム内に連続塗装ラインを設置して高品質で高効率の塗装を可能にしております。
脱脂効果の高い前処理工程
前処理での脱脂工程においては、最終工程に純水を使用することで、脱脂効果を高めております。
焼付乾燥炉で仕上げ管理
塗装後の焼付工程も、2基のバッチ炉とコンベア式山形焼付乾燥炉にて、ワンストップ対応いたします。最終外観品質までこだわりを持ち、仕上げ管理をいたします。
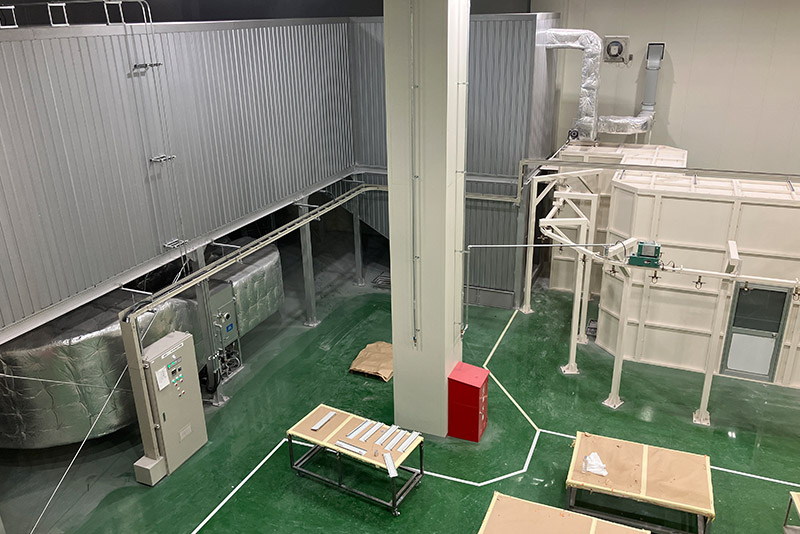
大物筐体用塗装ブース
コンベアラインに収まらない1m以上の板金部品や大型筐体は、バッチ式で塗装を行います。溶剤塗装、粉黛塗装、どちらにも対応しております。
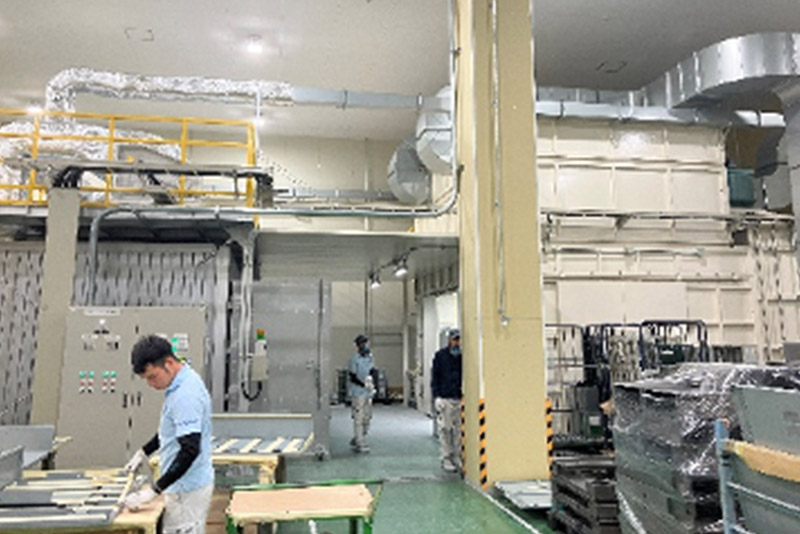
AIを活用した組立現場・ストックヤードを兼ねた部品倉庫
生産管理システムが完備されたフロアにて、多品種少量の精密板金筐体の仕上げ組立を行い、お客様に納期通りに高品質な製品をお届けいたします。生産情報をビッグデータとして収集し、AIで分析を行うことで、高効率生産を実現いたします。
また、組立後の板金筐体だけでなく、組立に必要な部品も取り揃える部品倉庫もございます。広大なストックヤードも兼ねており、100台以上の大型板金筐体の出荷調整も可能です。
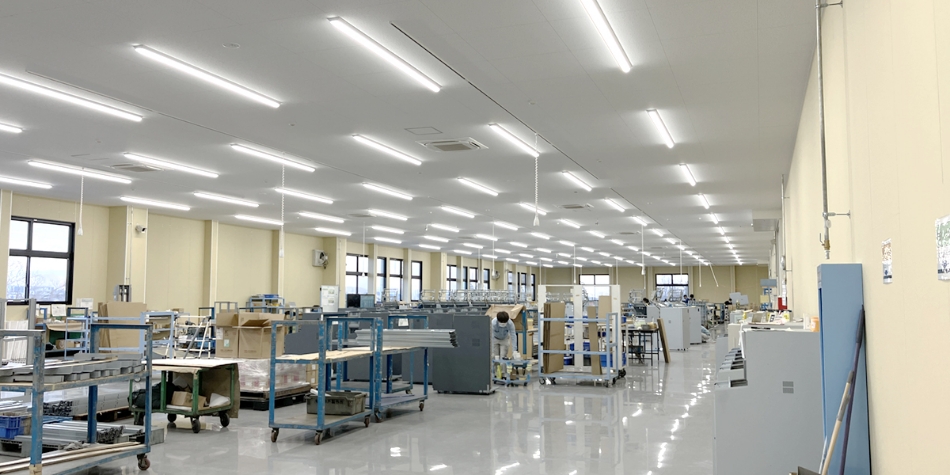
詳細は下記をご覧ください!
>>板金加工から塗装・組立までワンストップ対応!岡部工業の次世代工場「板金ソリューションファクトリー」
こちらのYouTubeでは、筐体板金の塗装工程を動画でご覧いただけます。